钢模板出租规格:建筑钢模板的技术革新与工业化应用
在城市化进程加速与建筑业转型升级的背景下,建筑钢模板凭借其高强度、可循环性和施工效率优势,逐步取代传统木模板,成为现代建筑工程的核心支撑体系。
在城市化进程加速与建筑业转型升级的背景下,建筑钢模板凭借其高强度、可循环性和施工效率优势,逐步取代传统木模板,成为现代建筑工程的核心支撑体系。从超高层建筑到装配式住宅,钢模板的应用贯穿混凝土结构施工全流程,推动建筑行业向标准化、工业化、绿色化迈进。本文系统解析建筑钢模板的技术特性、应用场景及未来创新方向。
一、建筑钢模板的核心技术优势
高强度与结构稳定性
建筑钢模板普遍采用Q355B、Q420C等高强钢材,抗拉强度达470-550MPa,屈服强度≥355MPa,可承受混凝土浇筑时产生的60-80kN/m²侧压力。例如,深圳平安金融中心建设中,采用桁架支撑的钢模板系统,单层浇筑高度达4.2米,模板最大变形量仅0.8mm/㎡,垂直度偏差≤1/2000,满足超高层核心筒的精度要求。模块化与快速施工
标准化钢模板(如P6015平面模板、Y1515阴角模板)通过U形卡、螺栓等连接件实现快速拼装。北京某装配式住宅项目中,6人班组可在3小时内完成200㎡墙板模板安装,施工效率较木模板提升50%。周转次数达50次以上,残值回收率超50%,全生命周期成本降低35%。表面质量与环保效益
激光切割(精度±0.2mm)与镀锌处理(锌层≥120g/㎡)技术确保模板表面粗糙度≤Ra1.6μm,混凝土成型可直接达到清水墙标准,减少抹灰层厚度30%。同时,电弧炉短流程工艺使吨钢碳排放降至0.8吨,较传统工艺减排62%。
二、典型应用场景与技术突破
高层建筑剪力墙体系
大钢模系统通过定型化设计覆盖整面墙体,与爬架协同实现“逐层攀升”。上海中心大厦采用6米高全钢大模板,单次浇筑面积1200㎡,施工周期缩短至3天/层,垂直累积误差控制在20mm内(总高632米)。装配式结构节点施工
预制叠合板:可调式边模通过磁力盒固定,实现板缝宽度±1mm控制,确保后浇带连接质量。
PC构件连接:三维可调模板系统精确定位预埋套筒,位置偏差≤2mm,满足装配式建筑“毫米级”精度需求。
复杂造型建筑实现
异形钢模板采用数控液压成型技术,可加工曲率半径0.5-15m的曲面结构。广州大剧院项目中,双曲面模板单元误差≤0.5mm/㎡,完美呈现扎哈·哈迪德设计理念,减少结构修整成本80%。
三、技术挑战与创新解决方案
轻量化与人工效率
薄壁高强钢(如2.5mm BS700MC)结合加强肋设计,模板重量降至22kg/㎡,人工搬运效率提升40%。
折叠式快拆模板(展开面积2.4㎡/块)适用于狭小空间,安装时间缩短60%(成都某地铁上盖项目数据)。
成本控制与资源循环
区域模板共享平台使周转率从40%提升至85%,南京某商业综合体项目通过租赁模式降低模板投入成本45%。
报废模板经破碎筛分后,95%钢材可回炉重铸,减少铁矿资源消耗50%。
智能化升级
BIM技术实现模板参数化设计,自动生成拼装方案,减少图纸错误率70%(雄安新区某智慧工地案例)。
物联网传感器实时监测模板形变,预警系统在应力达屈服强度60%时自动报警,提升施工安全性。
四、未来发展趋势
材料科技突破
钢-工程塑料复合模板(如Q355+聚丙烯)兼具强度与轻量化(18kg/㎡),周转次数突破100次,已在深圳某保障房项目试点应用。
记忆合金模板通过温度响应自动调节曲率,适应参数化建筑设计需求。
数字建造深度融合
3D打印钢模板技术实现24小时快速成型,复杂节点模板成本降低50%(西安建筑科技大学试验数据)。
数字孪生系统通过AR眼镜指导工人拼装,误差实时校正,培训周期缩短80%。
碳中和目标驱动
氢冶金工艺生产“零碳钢模板”,全生命周期碳排放减少90%(宝武集团2025年规划)。
光伏涂层技术使模板表面发电量达150W/㎡,满足施工现场20%用电需求(同济大学研发成果)。
结语
建筑钢模板的技术进化,既是建造方式从“手工劳作”向“精密制造”的跨越,也是建筑业可持续发展的重要实践。从超高层建筑的毫米级精度控制到装配式结构的工业化生产,从传统钢材到智能材料的突破,钢模板正在重塑建筑生产的DNA。预计至2030年,智能钢模板将覆盖90%以上的大型工程项目,推动建筑综合成本下降25%,为全球城市化进程提供高效、低碳的技术支撑。
热门文章
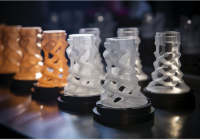
推荐文章